The Working Process
PUMOTIX allows you to flexibly adjust all the parameters of the oxy-fuel cutting process. Some parameters are monitored dynamically by the system, that is, changing a parameter immediately leads to a reaction of the control system. Another part of the parameters is applied not instantly, but before cutting each new contour (before executing the М03/М04 command).
Dynamically tracked parameters
PUMOTIX during heating and cutting allows you to change the following set of parameters and delays:
- preheat delay;
- preheat gas off delay;
- pierce delay;
- oxygen off delay;
- height adjustment speed.
Changing the value of any of these parameters during heating of the metal or cutting the contour will be instantly worked out by the system.
Parameters that apply to the contour
The remaining parameters of the workflow are not dynamically changing and are applied in the system before each new contour (М03/М04). The list of such parameters includes:
- cutting feed (working feed);
- probing speed;
- working cutting height;
- height of single crossings;
- probing radius;
- correction for nozzle height.
These parameters can be set and changed both before starting the G-Code, and during the execution of the program. The system will read the parameters each time before processing each successive contour of the part (that is, before executing macros to start ignition, heating and cutting torch M03/M04).
Auto-ignition and warm-up controls
The control of the burner ignition process (if there is an automatic ignition system) and metal heating is carried out on the main working tab of the module - the “Workflow Process” tab.
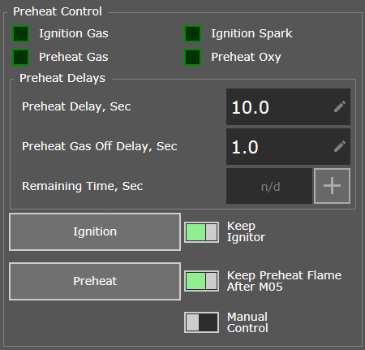
Ignition and heating control unit
Indication
A set of indicators in the upper part allows you to monitor the status of outputs reserved for valve and spark gap control. When the gas or oxygen valve is open, the indicator is colored green, and when closed, it is black. The indicators show the status of the following signals:
- pilot gas valve (gas supply to the auto ignition system);
- ignition spark activation output (control output of the spark ignition system of the automatic ignition system);
- warm-up gas valve (supply of warm-up gas to the torch);
- warm-up oxygen valve (supply of warm-up oxygen to the torch).
Time delays
To provide flexibility in controlling the heating procedure of the metal, the oxy-fuel cutting module allows you to configure the following time delays:
- Preheat Delay
The duration of metal heating depends on many factors: thickness and type of metal, ambient temperature, gas quality, etc. Therefore, the exact value of the heating time may not be known in advance. When the operator does not know the duration of the warm-up, the system can be switched to the manual control mode of heating (“Manual control” switch). In this mode, heating will not be interrupted automatically by timer. The system will run the actual warm-up time in the “Elapsed since launch” field. As soon as the operator decides that the metal is sufficiently warmed up and can proceed to cutting, he must manually complete the heating. Manual interruption of heating is available in two versions:
1. only complete warm-up;
2. Complete warm-up and save time.
In the first case, the heating will be immediately interrupted and the system will proceed to supply cutting oxygen. If the warm-up is completed with time being saved, the system will interrupt the warm-up and save the actual duration of the current warm-up session to the “Warm-up duration” parameter. Thus, the system can be trained on this parameter. To automatically warm up with the time saved before cutting subsequent circuits, the system must be brought out of manual control mode by putting the switch in an inactive state.
In the automatic heating control mode, it is possible to extend the current warm-up session with the “+” button. One press of the button adds 5 seconds to the remaining time. The parameter "Duration of heating" remains unchanged. If necessary, you can save the actually obtained warm-up time with the button “End warm-up and save time". - Prehaet Gas Off Delay
The parameter responsible for the delay immediately after closing the heating gas valve before turning off the oxygen supply. The delay between turning off the gas and oxygen is necessary to prevent back impact and purge the torch channels with oxygen. When a warm-up shutdown command is issued, the system first closes the gas supply valve, performs the specified time delay, and closes the oxygen supply valve. You can track the status of gas and oxygen valves using the appropriate indicators on the main program screen.
Process control buttons
- "Ignition" button
Turns on or off the automatic gas burner ignition system. When ignition is turned on, the system performs the following actions:
1. opens the gas valve to the ignitor;
2. expects a time delay after the start of gas supply (set in the menu "Configuration" → "Settings" → "Oxy-Fuel" → "Ignitor settings");
3. activates the output of the spark;
4. expects the duration of the spark supply (set in the menu “Configuration →“ Settings ”→“Oxy-Fuel”→“ Ignitor settings ”);
5. deactivates spark output.
Gas will be supplied to the burning burner of the auto ignition system until the main burner is ignited. After ignition of the main burner, the system will automatically turn off the auto-ignition burner.
It is possible not to turn off auto ignition. Activation of this function is carried out by transferring the “Do not turn off ignition” switch to the active state. - "Preheeat" Button
It ignites or extinguishes the main gas burner of the machine. When a warm-up enable command is issued, the system performs the following
actions:
1. starts the ignition procedure if the automatic ignition control signals are configured or the auxiliary automatic ignition burner is not already ignited;
2. opens the heating gas supply valve;
3. opens the warm oxygen supply valve.
The burner is set on fire in warm-up mode. Only heating gas and oxygen are supplied. Counting the duration of the warm-up at this stage is not performed.
Disabling warm-up occurs as follows:
1. closing the heating gas valve;
2. waiting for a delay after turning off the warm-up gas;
3. closing the warm oxygen supply valve. - The switch "Keep Ignitor"
In the active state, instructs the system to hold the auxiliary burner of the automatic ignition system lit. In the inactive state, the auto-ignition burner will be extinguished immediately after ignition of the main burner. - The switch "Keep Preheat Flame After M05"
In the active state, it prohibits the system from turning off the supply of heating gases to the torch. Use this function if you do not want to completely extinguish the cutter with the torch shut off command (M05). If the option is disabled, after cutting each circuit in the control unit, the system will completely extinguish the burner. - Manual Control Switch
Changes the system from automatic heating control mode to manual. Manual mode is useful when the exact warm-up duration for working in automatic mode is not known. Warming up will be carried out indefinitely, until it is interrupted by the operator manually. The countdown of the actual time elapsed since the start of warm-up will be displayed on the screen. As soon as the operator determines that the metal is sufficiently warmed up (as a rule, visually), heating must be interrupted in the required mode (training - saving the actual time in the variable “Duration of heating” or only completion). After that, the system will go to the next stage - supplying cutting oxygen, holding the duration of burning and moving along the contour of the part.
In the inactive state of the switch, the warm-up system works automatically according to the parameter "Warm-up duration".
Cutting controls
The metal cutting process is controlled on the main working tab of the module - the tab "Workflow Process".
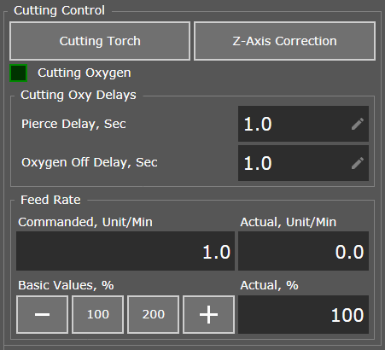
Cutting control unit
Indication
The "Cutting Oxygen" indicator allows you to monitor the status of the cutting oxygen supply valve. When the valve is open and purge oxygen enters the torch, the indicator is active.
Time delays
To provide flexibility in controlling the metal processing procedure, the oxy-fuel cutting module allows you to configure the following time delays:
- pierce delay, s
Waiting time for burning (purging), during which the torch will stand above the metal with the cutting oxygen supply turned on. The countdown of the piercing duration begins immediately after the expiration of the warm-up delay. After the piercing time has passed, the torch will begin to move along the part contour. - oxygen off delay, s
Turning off the supply of cutting and heating gases at the same time is not allowed. The delay after cutting oxygen shutdown is a parameter responsible for the pause immediately after closing the cutting oxygen valve before the start of the shutdown of heating gases. When a cutting torch shutdown command is issued, the system will turn off the cutting oxygen supply, perform the specified time delay, and proceed to the heating gas shutdown routine (if required). You can track the status of the valves using the appropriate indicators on the main program screen.
Process control buttons
- Cutting Torch Button
Serves for giving the command to enable or disable the supply of gases that ensure metal cutting. The complete torch ignition cycle is performed by the “Cutting torch” button, as well as the M03/M04 macros, both from the unitary enterprise and using the manual G-code entry line. The full torch ignition cycle includes a number of sequential commands:
1. ignition;
2. warming up;
3. cutting torch.
Ignition is an internal subroutine of the system, the result of which is the ignited auxiliary candle of the automatic ignition system. This candle is used to ignite the main burner. The main burner is ignited by the “Warm up” command.
The warm-up command calls the internal subroutine of the ignition of the main burner of the machine. If the automatic ignition system is present in the system, but the auxiliary burner has not yet been ignited, then the “Ignition” command will be executed first and only after that the “Warm-up” command will be executed. After executing the “Warm-up” command, the system will supply heating gas and oxygen to the torch until a command to turn off the warm-up is received.
The “Cutting torch” command is a call of three subprograms: ignition, heating and supply of cutting oxygen. The call of the ignition and warm-up routines is always performed if necessary, since the supply of cutting oxygen to the unlit cutter is prohibited. Thus, the system always performs strictly sequentially the supply of ignition, heating and cutting gases. Situations when the system opened the cutting oxygen valve, but the cutter was not set on fire, are excluded. Likewise, warm-up cannot be turned on if the control signals of the automatic ignition system are configured, but the auto-ignition candle is not ignited. In this case, warming up will start with auto ignition, etc. - Button "Z-Axis Correction"
Activates or deactivates the monitoring of the surface of the metal - correction of the height of the Z axis. Adjustment of the physical distance between the gas cutter and the workpiece during cutting, as a rule, is carried out by measuring the capacitance and generating corrective signals "Up" and "Down" depending on the measured result. The correction mechanism differs depending on the selected Z-axis control mode. In the autonomous Z axis mode, the height control is completely controlled by the autonomous axis equipment. The “Z-Axis Correcton” button in this mode only allows the system to control the “Correction signal output” (“Capacity” signal), which is transmitted to the autonomous axis control unit. In the Z-axis control mode via the Up/Down protocol, the “Z-Axis Correcton” function allows the system to ignore or monitor the status of the Up and Down control inputs transmitted to the system from an external controller. In manual control of the Z axis, this function enables or disables Z height correction using the Up and Down buttons on the program screen.
Feed controls
The feed specified by the “Desired, unit/min” parameter is the speed of the torch moving along the part contour during the cutting process. The change of this parameter is read by the system before cutting the next contour of the part (during a call М03/М04). To change the speed of movement along the contour directly during cutting of the contour, it is necessary to use the “Quick Install” buttons or the horizontal feed rate override slider (FeedRate Override). Available range of change: 0% - 200%.
Simulation mode
The simulation mode allows you to perform the UE without turning on the torch with a given feed and height.
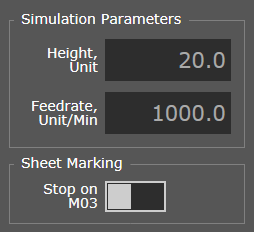
Simulation Mode Options
If the “Stop on M03” option is active, the simulation will pause at each burn point until the “Start” button is pressed. The torch will be located above this point. This mode can be used to manually mark tie points.