Настройка параметров резки
Рабочий процесс
PUMOTIX позволяет гибко настраивать весь набор параметров процесса плазменной резки. Часть параметров можно менять динамически, то есть в процессе резки металла. Остальные параметры применяются перед каждым новым контуром резки (перед вызовом макроса M03/M04).
Динамически изменяемые параметры
Непосредственно во время резки материала PUMOTIX позволяет изменять следующий набор параметров:
- напряжение (желаемое);
- превышение напряжения;
- скорость регулирования Z;
- минимальная скорость для регулирования;
- минимальное значение коррекции;
- максимальное значение коррекции.
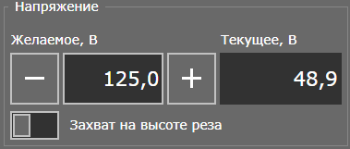
Установка и мониторинг напряжения
Так же в процессе выполнения УП у оператора есть возможность изменения текущей скорости резки, с помощью элементов управления скоростью на главном экране. Доступный диапазон изменения: 0-200% от желаемой скорости.

Установка и мониторинг скорости
Изменение параметра «Желаемое, ед/мин» будет принято перед резкой следующего контура (то есть перед очередным макросом M03/M04).
Остальные параметры
Все оставшиеся параметры не являются динамически изменяемыми и применяются в системе перед каждым прожигом:
- скорость резки;
- высота начала пробинга;
- скорость пробинга;
- высота поджига дуги;
- длительность прожига материала;
- рабочая высота резки;
- длительность переноса дуги;
- высота холостых переездов;
- радиус пробинга;
- поправка на высоту сопла;
- делитель напряжения;
- задержка регулирования;
- диаметр трубы;
- высота «Умного прожига»;
- радиус дуги для снижения скорости;
- снижение скорости (%).
Эти параметры можно устанавливать и изменять как перед запуском УП на выполнение, так и в процессе выполнения УП. PUMOTIX считает и применит измененные параметры перед началом следующего прожига.
Захват напряжения на высоте реза
Система управления плазменной резкой PUMOTIX позволяет использовать функцию автоматического захвата напряжения в дуге. Данная опция полезна в том случае, если оператор станка точно не знает, какое желаемое напряжение должно быть выставлено для резки данного материала, но знает рабочую высоту, которую необходимо поддерживать в процессе всей резки. Таким образом, при активной опции «Захват на высоте реза» система будет использовать напряжение в дуге, установившееся к началу регулирования высоты Z. Данное напряжение будет измерено блоком THC автоматически и записано в параметр «Напряжение (желаемое), В». При включенной опции «Регулирование Z» система будет поддерживать захваченное напряжение до конца резки контура.
Активация опции производится кнопкой «Захват на высоте реза» или автоматически, если в поле параметра «Напряжение (желаемое), В» установлено значение 0 вольт.
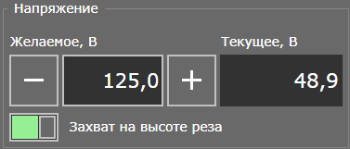
Захват на высоте реза
Кнопки управления рабочим процессом
На главном экране «Резка» в группе «Рабочий процесс» также расположен набор кнопок управления некоторыми функциями плазменной резки:
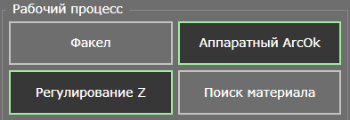
Кнопки управления рабочим процессом
- Кнопка «Факел» служит для отправки включения и выключения факела плазмотрона. При выполнении УП, как правило, вручную факел не включается. Включение факела производится макросами М03/М04 непосредственно из УП. Включение факела плазмотрона кнопкой применяется при резке металла в ручном режиме (перемещение осей кнопками с экрана или клавиатуры). Для быстрого включения/ выключения факела с клавиатуры можно использовать горячую клавишу F5.
Дополнительной функцией к ручной резке металла является функция копирования желаемой подачи в скорость ручных перемещений. При активации данной функции система автоматически переключит режим ручных перемещений со скопированной скоростью подачи. Достаточно лишь подъехать к желаемой точке старта ручной резки, включить «Регулирование Z» (если оно необходимо), активировать Факел и выполнить резку контура с помощью клавиатуры.
Кнопка «Скопировать желаемую подачу» располагается на главном экране в блоке управления ручными перемещениями.
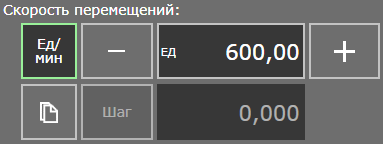
Применить подачу для ручных перемещений
- Кнопка «Аппаратный ArcOk» включает/выключает использование сигнала ArcOk — сигнала переноса дуги. Данный сигнал формирует блок аппарата плазменной резки (АПР) при удачном переносе дуги. Когда опция «Ожидание ArcOk» включена, PUMOTIX выполнит команду розжига дуги и перейдет в режим ожидания сигнала ArcOk. Как только сигнал будет получен от плазменного блока, PUMOTIX продолжит завершение процедуры розжига и выхода на рабочую высоту резки. В случае потери сигнала ArcOk в процессе резки контура (дуга потухла), выполнение программы будет прервано.
При отключенной опции «Ожидание ArcOk» система управления PUMOTIX работает с параметром «Длительность переноса дуги» (см. описание параметра в предыдущей главе). Отключение данной опции имеет смысл в том случае, если в используемом АПР нет вывода сигнала ArcOk. - Кнопка «Регулирование Z» включает/выключает коррекцию высоты резака над материалом путем удержания желаемого напряжения. Регулировка физического расстояния между резаком и заготовкой при резке выполняется в зависимости от напряжения плазменной дуги. Механизм регулирования заключается в том, что контроллер THC передает по сети Ethernet действующее напряжение в дуге. ЧПУ контроллер принимает эту информацию и производит корректировку высоты, после чего передает в PUMOTIX текущее состояние корректировки. Таким образом, контроллер знает не только требуемое направление корректировки, но и величину отклонения от номинала, из которой можно определить требуемое смещение оси Z в данный момент времени. Благодаря этому обеспечивается высокая точность поддержания высоты реза, что положительно влияет на резку без окалины, внешний вид среза и стабильность размеров детали.
- Кнопка «Поиск материала» запускает алгоритм поиска поверхности материала. Предварительно должен быть настроен сигнал датчика Probing в разделе «Настройки» → «Сигналы» → «Параметры входных сигналов». Будет произведен поиск поверхности металла, обнуление координаты Z и подъем на безопасную высоту (значение параметра «Высота холостых переездов»). Если сигнал с датчика не был получен по окончании поиска материала, система выдаст соответствующее сообщение.
Режим симуляции
Режим симуляции позволяет выполнить УП без включения факела с заданной подачей и высотой.
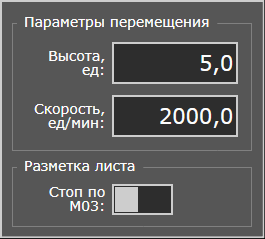
Параметры режима симуляции
При активной опции «Стоп по M03» симуляция будет приостанавливаться в каждой точке прожига до нажатия кнопки «Старт». Резак при этом будет располагаться над точкой пробивки. Этот режим может использоваться для ручной маркировки точек врезки.