General Settings
On the “General” tab, you can select the server to connect to. Client-server architecture allows you to connect both to a server running on the local machine and to servers on other computers (automatic server search and manual server parameters are available).
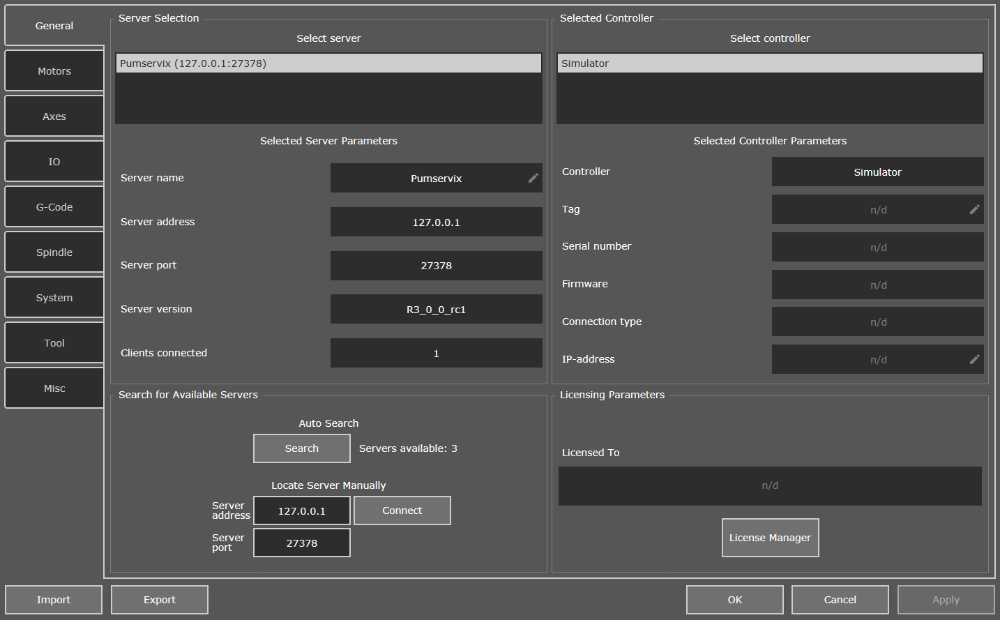
“General” Tab
Setting the parameters of motors and axes is one of the most important parts of tuning the CNC system. The motor in the context of the PUMOTIX control program is a physical unit, i.e. the machine's actuator (step drive, servo drive, etc.). An axis is a logical unit of a system that is connected to a specific set of motors. One or more motors can be attached to any axis.
The concept “Motor” includes such concepts as Step/Dir/Enable outputs, home (zero) sensors, axis boundary sensors, as well as the axis to which this motor is attached. Adding a new motor and setting parameters is carried out on the “motors” tab.
After selecting the server, you must select the device in the list on the right. After that, PUMOTIX will automatically check and, if necessary, update the controller firmware version. In this case, the message “Device found. The firmware is being updated. ” This procedure may take up to two minutes.
For each of the devices, you can configure the IP address and subnet mask by clicking on the button in the "IP address" line.
Obtaining an address from a DHCP server should be used if there is a DHCP server on your local network (a device that can dynamically assign IP addresses can be a regular home network gateway to access the Internet).
If your network does not have a DHCP server that assigns IP addresses, select "Use the following IP address" and set the IP address manually.
The “Export” button at the bottom of the window allows you to save device settings (assignment of inputs and outputs for motors, axis parameters). Then you can connect another device and load the settings into it using the “Import” button.
On the “Motors” tab, you can create up to 6 motors, each of which can be connected to any of 9 axes. The outputs Step, Dir, Enable, inputs Home, Limit Low, Limit High are configured for each motor. In general, setting the parameters of motors is similar to setting other CNC systems to work with PLCM series controllers.
PLCM controller configuration reset can be performed by pressing the “Factory reset” button on the basic settings tab. After resetting the settings, the default configuration is loaded into the PLCM, including motor settings, axis settings, input and output signal settings. You may also need to reconfigure the device IP address.